2018-07-03
“Our benchmark is the life cycle of the product”
Mechanical cable manufacturer RINGSPANN RCS convinces with quality and customer orientation
When it comes to the implementation safety-relevant unlocking, emergency trigger or release systems, RINGSPANN RCS push-pull cables are the first choice for operators in a wide range of sectors. That is not only down to the high quality of the mechanical actuation and operation elements from Oberursel, but also the company’s unwavering customer orientation. In an interview, managing director Christian Kny also explains why he is particularly focused on the optimisation of the service lifetime of the cable systems.
RINGSPANN RCS is viewed as a premium manufacturer of high-quality push/pull cables and currently quite possibly boasts the most innovative product range on the market. Its mechanical control, actuation and operation elements are also currently subject to healthy demand. You could easily lay back and relax now, couldn’t you?
Kny: That may all be true, but there can be no question of us resting on our laurels. While we may already cover a broad spectrum of applications with our four cable models and our wide range of standard sizes, forces, travels and attachment parts, the constant striving for technical improvements never lets us rest. Furthermore, we have clients approaching us almost daily with new demands. And of course, we cannot forget the competition.
Aren’t push/pull cables standard elements whose technical development has long been concluded?
Kny: No, it just looks like that at first glance – particularly if you mistake our products for traditional Bowden cables. Our cable systems are demanding mechanical remote control systems for alternating power transmission with in some cases extremely complex designs. They are suitable for all applications where forces need to act between spatially separated, fixed modules, and where it must be possible to separate the connection of input and output force through a flexible system. Our cables are intrinsically safe, maintenance-free, extremely flexible, protected against splash water and convince thanks to excellent sliding properties. They may be among the best on the market; and yet that doesn’t stop us from constantly working to improve them. Whether it is about tribological aspects, the use of new materials or innovative reinforcements – we are working on many fronts.
Can you give our readers a specific example of this?
Kny: The push-pull cables of our current premium 380 series are not just a result of many decades of practical experience and a high degree of manufacturing expertise, but in terms of the materials used and the constructional implementation – also in detail – they are a real premium product. This bi-directionally operating Bowden cable works safely even at high loads, with small bending radii and at constant temperatures of -50° C to 100° C and exhibits very smooth operation. The engineer thus receives a first-class remote control system with a high degree of effectiveness and a response behaviour that is unrivalled on the market and furthermore does not exhibit any stick-slip effect – always provided that the selection was carried out carefully and that no errors were made during installation and use.
Errors during installation and use? What are you thinking of specifically?
Kny: Only recently, a renowned automobile suppliers conducted a comprehensive benchmarking with push-pull cables of all internationally relevant providers with our RCS cables emerging as the winner. Best performance, best response behaviour, best back lash – all first class! However, we wondered about the fact that our push-pull cable was said to break on the test bench after 600,000 actuation cycles – when they are in fact designed for 1.0 million cycles. Since that did not seem right, we took a closer look at the test setup on site. It was here that we discovered the clamping device had damaged the conduit cap of our cable; the push-pull cable had thus been in an unfavourable enforced state during testing. It was therefore rather astonishing that it even managed to complete 600,000 cycles. We are also often confronted with unrealistic force demands. Recently, I read for example in a product specification that our cables should be designed for manual pushing forces of 6,500 N. When I then asked the manufacturer which weightlifter he envisaged as a potential operator, we both had to laugh …
What exactly is this stick-slip effect you mentioned?
Kny: It refers to the constant switching between stick-slip and gliding, usually at lower speeds. It would be perceptible as a jerking motion and would thwart the transfer of force. To rule out this negative effect, the cable systems in the 380 series are not only equipped with a spiral-supported flat-wire reinforcement, but also with Teflon-coating and a finely tuned inner tube in the conduit. Our heavy-load cables from the 280 series for pushing forces of up to 1,350 N and pulling forces of up to 4,500 N also have this feature. It minimises sliding friction and makes it possible to achieve very small bending radii – for example for confined installation locations.
Which factors should an engineer primarily take into consideration in the selection and design of RCS cable systems?
Kny: He may already know some base values, such as the required pushing and pulling forces, anticipated deployment temperature or the required vertical travel; when it comes to other factors, it is advisable to bring us into the fold as early as possible – already in the testing phase. Many questions can only be answered accurately if we know the specific application. This has an impact for example on the suitable design of the end parts – zinc-coated or rust-free –, the best connection type of the cable – swivelled, rigid, screwed or clamped – or on the design of the wiper seal. It is also important to know which routing the cable needs to be designed for.
Now that really does sound like a lot of detailed work to determine the optimal power cable…
Kny: … yes, that is often underestimated. I can only advise against carelessness when it comes to the technical design and dimensioning of push-pull cables; also, I strongly advise against ordering from online catalogues of unknown providers. You should particularly focus on two things: Firstly, as fire-and-forget solutions, the cable systems should be able to carry out a very large number of travels over a long period of travels safely, maintenance-free and smoothly. And secondly, many applications require that cables must always immediately deployable despite very long, idle standby phases. This is incidentally the reason why RINGSPANN RCS prioritises the optimisation of the product life cycle over optimising production times.
Oh, now that is a surprise; how can we understand that?
Kny: Naturally, we take a systematic approach towards the continuous improvement of our manufacturing efficiency, that goes without saying. In terms of the high quality of our products and their utility for the customer, our primary benchmark, however, is the optimisation of the life cycle of our cable systems – particularly through innovations in the areas of prolonging service life, lifetime extension and functional safety.
But don’t all providers make the same claim?
Kny: That may be the case. However, while some manufacturers invest a great deal of energy and money in autonomous full automation to be able to manufacture ever larger quantities of identical standard cables more quickly, the focus of RINGSPANN RCS lies in continuously improving the quality of the cable systems themselves. In order to do so, however, you have to place the emphasis on development work and in production employ a flexible mix of manual, craftsmanship-style production and industrial mechanised assembly. The fact that we have been able to achieve this is in some ways our key to success. It also puts us in the position of being able to achieve a high level of customer orientation in the day-to-day business.
Nowadays companies all have a different definition of the term “customer orientation”…
Kny: … we are always looking at a two-fold perspective in this regard: Our primary customer is the engineer or purchaser in the sports car divisions of automobile manufacturers, in marine engineering, in aircraft construction or robotics and fluid technology, who for example needs a remote-control solution for a new locking and unlocking system or an alternative to a complicated linkage device. Or just a better, fail-safe mechanical cable. However, our customer is also the end user who uses our push-pull cables in practice – in the case of motorsports, for example, very successfully so. Ultimately, we always need to keep both happy. And this does not work with standard cables bought “off the shelf”; it requires experience, engineering expertise and flexibility in production – and here we are now able to offer an interesting intermediate solution.
Now we’re curious. What exactly is this “intermediate solution”?
Kny: Our great strength – also unlike many competitors – is founded in our high level of expertise in the development and engineering of customer and user-specific cable system solutions. Thanks to our company history, we are able to draw on a large pool of specialist topics such as kinematics and tribology and a wealth of practical experience in the field. However, if there is no need or if there is a lack of time to conduct a development project, we also offer the option of customer-specifically coordinating and configuring common types of push-pull cables from the RCS standard range from certain batch sizes. Thanks to our extensive range and flexible manufacturing structure, we are often quickly able to achieve excellent results.
And how do you react in urgent cases, i.e. if time is of the essence?
Kny: Besides the fact that we are always able to deliver the most frequently requested variants of our cable systems from the catalogue range at short notice, a few weeks ago we launched our new express cable offer. Here, our million-selling product – a 280-series push-pull cable – is already available upon demand via 24/7 rapid delivery service. This cable for pushing forces of up to 320 N and pulling forces of up to 540 N is equipped with a flat-wire reinforced and Teflon-coated inner member, connection parts made of stainless steel and seals against dust and moisture – it is thus already a high-quality RCS premium product. It is available with immediate effect with and without a T-grip.
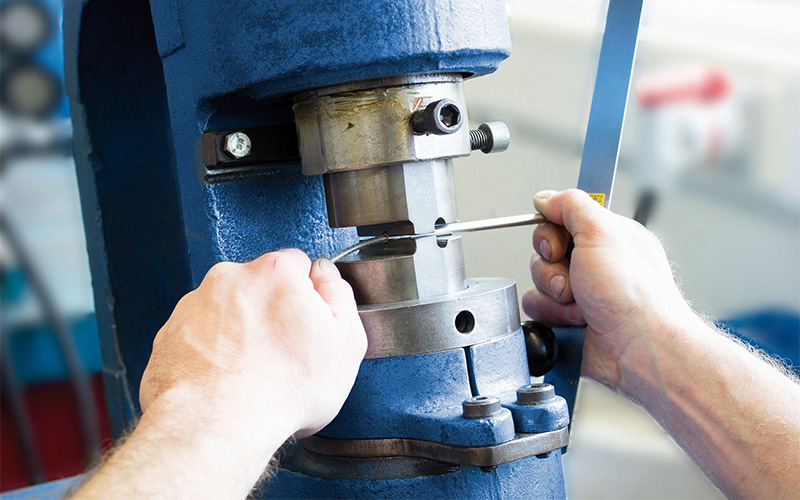
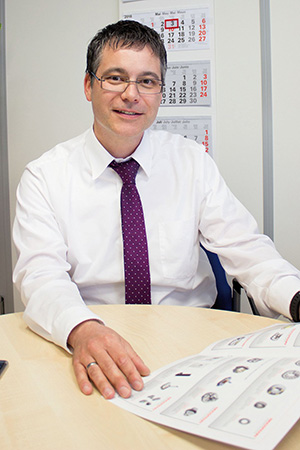
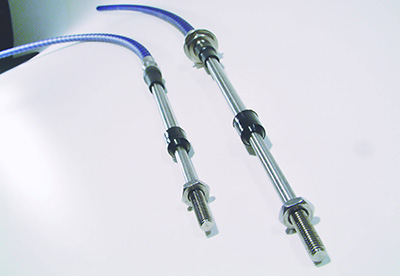
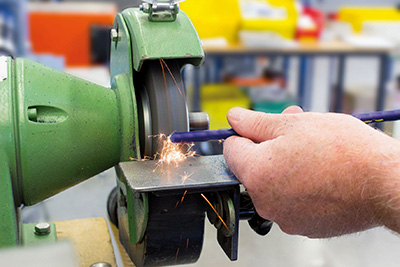
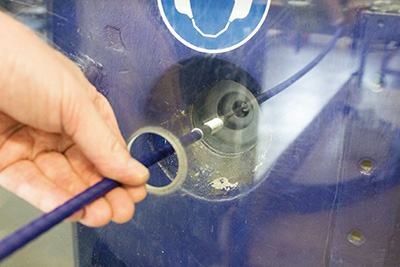
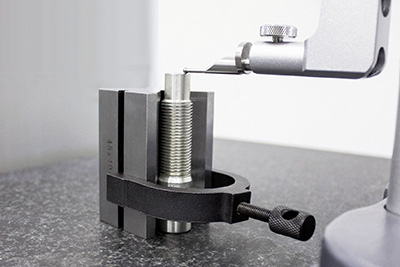
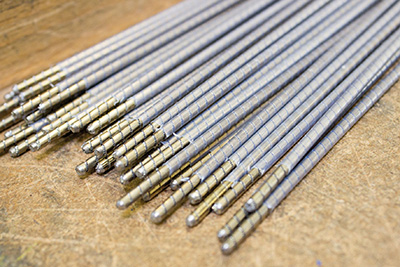
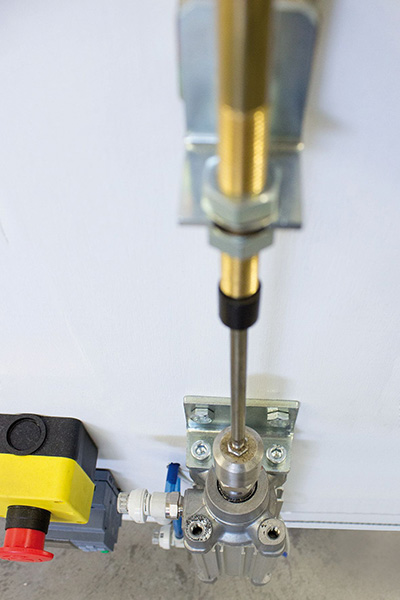