2021-04-26
Innovative clamping systems for gearing technology
RINGSPANN presents special skiving clamping fixtures with optimised chip removal
Precision clamping fixtures for the complete machining of thin-walled lightweight components and high-precision internal clamping systems for use in gearing technology – just one reason as to how RINGSPANN has recently consolidated its position as an OEM supplier for machine tool manufacturers. Now the Germany company is surprising the industry with another innovation: high-performance diaphragm and taper sleeve clamping systems that are specially tailored to the requirements of the currently very popular power skiving process for the production of high-precision external and internal gears.
Bad Homburg, April 2021. – As an alternative to gear hobbing, gear shaping and broaching, skiving is enjoying renewed interest in the domain of gearing technology. Increasing quality and productivity demands in gear manufacturing in particular are reviving the interest of machine tool manufacturers and e-drive producers in the manufacturing principle developed more than 100 years ago. Why? The process not only meets high standards of precision and accuracy but is also proving to be an extremely economical method for the cutting soft and hard machining of internal and external gears in the face of growing demands for batch size flexibility in series production. In addition, innovative leaps in control technology, high-performance machining and machine statics are fuelling the entry of skiving into the production processes of gear manufacturers and gear suppliers. While other gearing processes have to be used on special machines, power skiving can be used within the scope of complete machining in modern 5-axis centres. Accuracy losses due to multiple clamping can be reduced, as well as machining and set-up times.
Deformation-free clamping
However, the many advantages of skiving can only be fully realised in the practice of gearing technology if suitable clamping systems are used on the machines. This is because power skiving is characterised by a precisely positioned skew between the driven workpiece and tool axes (axis intersection angle) and the synchronisation of both speeds. The adjustment of the tool with a defined axial feed and the speed coupling of the workpiece and tool result in a relative movement with which the free space between the teeth is peeled into the material. In order for this to take place disturbance-free and with very short machining times (up to 50 per cent faster than with gear hobbing), the clamping systems used here must be balanced for high speeds and guarantee problem-free chip removal.
The diaphragm and taper sleeve clamping systems from RINGSPANN, which have been further developed for skiving, are precisely tailored to these requirements. They are particularly predestined for the internal gear cutting of thin-walled workpieces that must not deform under any circumstances during machining – for example weight-optimised toothed rings for planetary gears. In this application, for example, they replace conventional jaw chucks.
Open for safe chip removal
"Both versions of RINGSPANN’s skiving clamping systems are based on fundamental functional principles that have proven themselves in gearing technology over a number of years", says Volker Schlautmann, head of the company’s clamping fixtures / shaft-hub-connections customer team. Typical of their design is a relatively open construction, which enables rapid chip removal. Characteristic of the diaphragm clamping systems are a short overall length and a very uniform application of the clamping forces on the workpiece. They also offer the possibility of clamping on the shortest clamping surfaces. The key features of the taper sleeve clamping systems, on the other hand, are the large clamping depth and an impressive degree of rigidity. In both cases, the frictional connection is made via workpiece-encompassing clamping elements, which can be quickly and easily exchanged during changeover. RINGSPANN supplies both versions ready for use, balanced and, if required, with air system control.
Added benefit in the process
The e-mobility boom in particular is causing a significant rise in demand for planetary gears. This is currently leading to growing interest in internal gears that can be manufactured very efficiently via skiving. The use of RINGSPANN’s diaphragm and taper sleeve clamping systems can help both gear suppliers and gear manufacturers to fully exploit the productivity and flexibility benefits of this process. Machine tool manufacturers, on the other hand, who offer skiving as part of complete multi-axis machining, can offer their customers RINGSPANN clamping systems as an added benefit within the scope of process integration. ms
RINGSPANN’s skiving clamping systems at a glance
Diaphragm clamping system for internal gears:
- Lightweight construction
- Power or manual operation
- Clamping with draw-down effect
- Air system control in contact bolt or backstop ring
- Open design optimises chip removal
Taper sleeve clamping system for internal gears:
- Power operation
- Clamping with draw-down effect
- Air system control in contact bolt or bearing ring
- Open design optimises chip removal
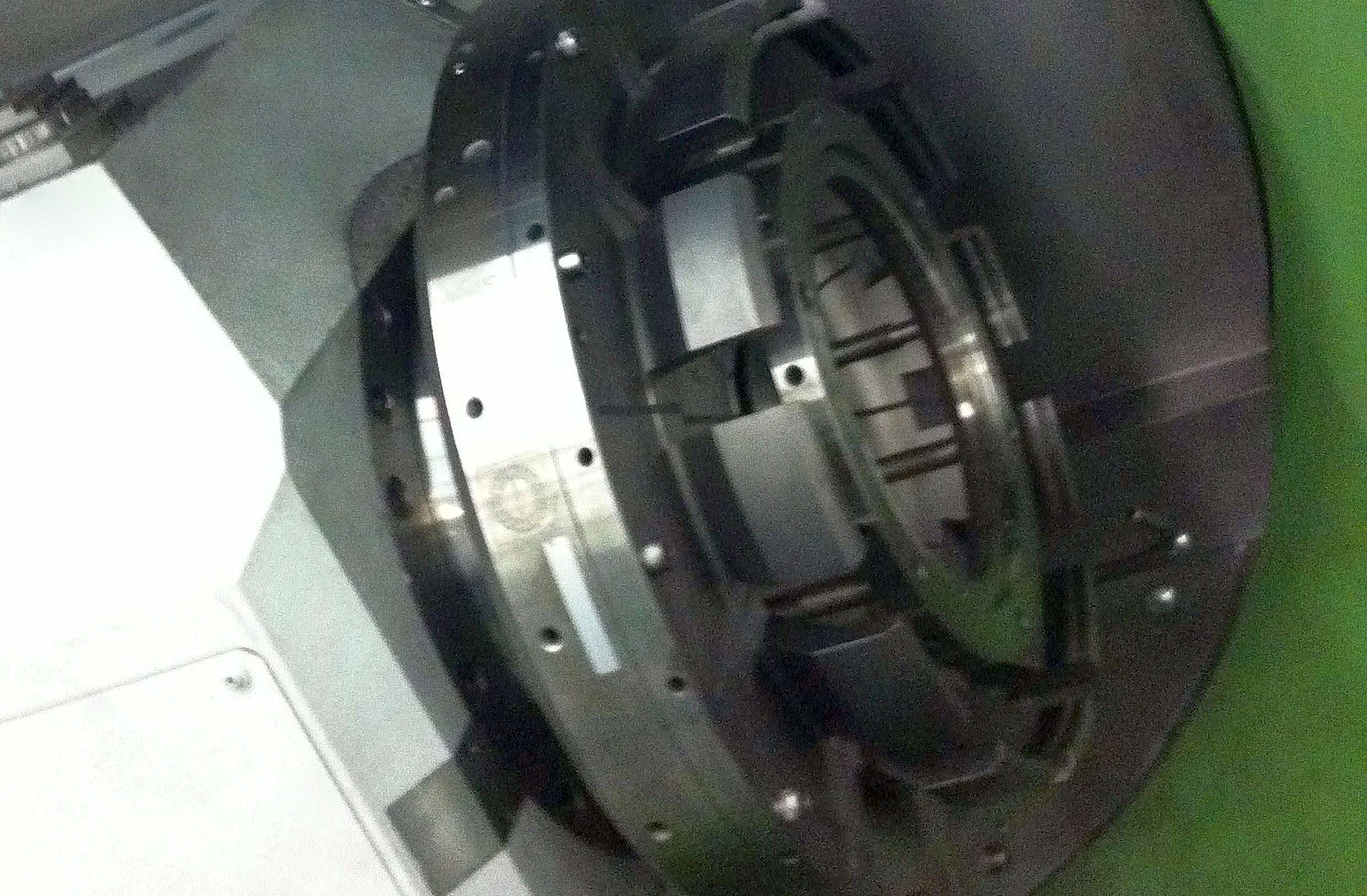
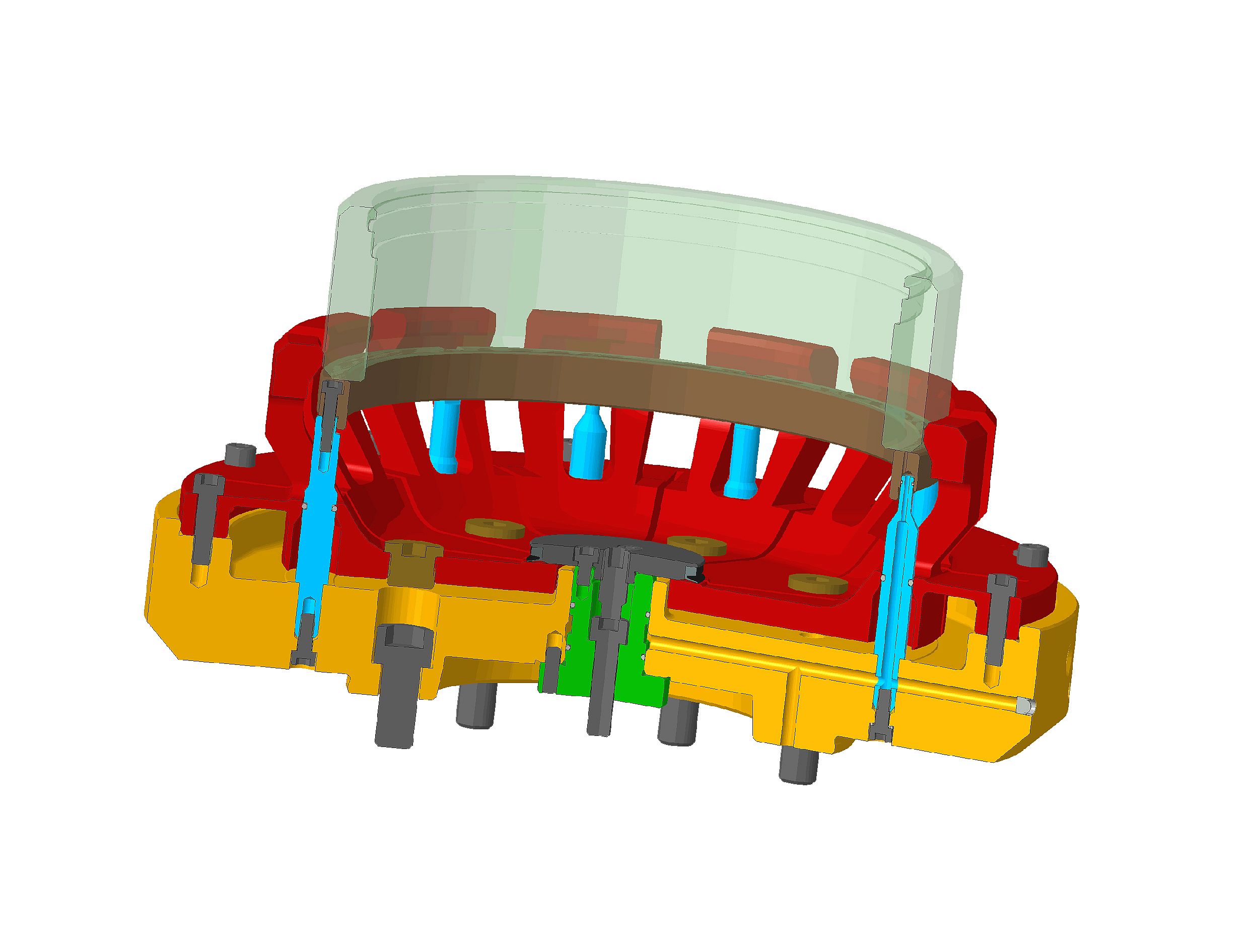
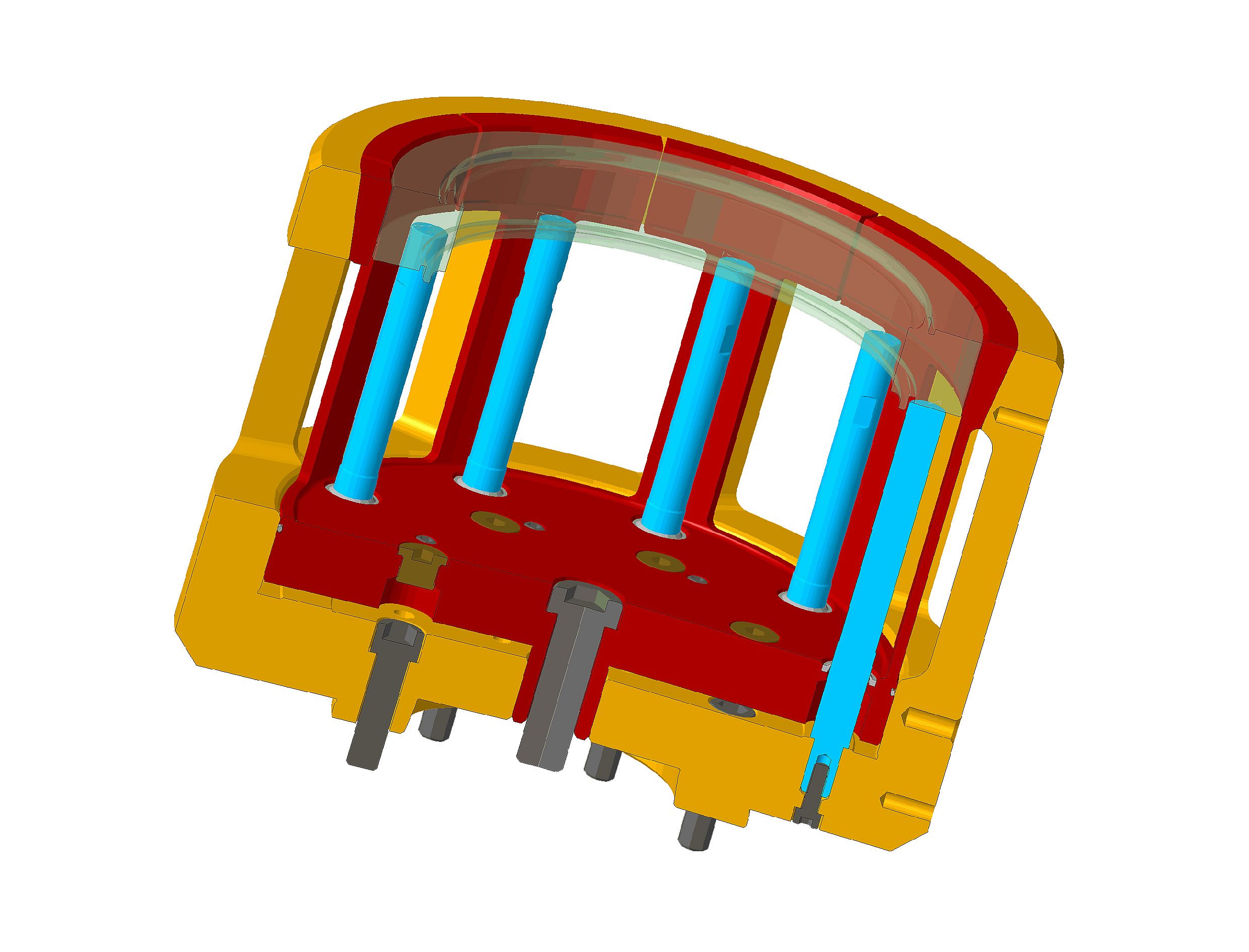
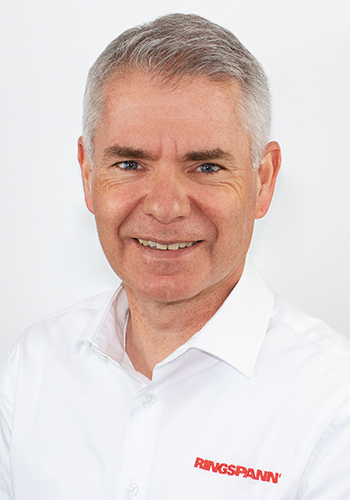